轮廓度误差检测及计算方法介绍
安徽省产品质量监督检验研究院 陈昌琼
地址:安微省合肥市包河区延安路 号 邮编:
【摘要】 所谓轮廓度是指被测实际轮廓相对于理想轮廓的变动情况。这一概念用于描述曲面或曲线形状的
准确度。其中轮廓度包括面轮廓度与线轮廓度本文笔者根据 多年的工作积累,对典型的轮廓度常用测量
方法的进行剖析及其计算方法的介绍。希望读者能从中得到启发,能运用到以后的工作中去。
【关键词】:轮廓度误差 面轮廓度 线轮廓度 公差带
引言
任何零件的面都是由平面和曲面组成的。曲面形状误差的检测和评定也是产品检验中一个非常重要的项
目。在机械制造业中,用轮廓度指标评定其误差大小。轮廓度分为统轮廓度和面轮廓度本文主要针对轮廓度的知识及误差用三坐标检测方法等内容进行介绍。轮廓度公差的相关概念
线轮廓度公差的定义 线轮廓度是限制实际曲线对理想曲线变动量的一项指标,它是对非圆曲线的形状精度要求。线轮廓度公差是实际被测要素(轮廓线要素)对理想轮廓线的允许变动。
面轮廓度公差的定义 是限制实际曲面对理想曲面变动量的一项指标,它是对曲面的形状精度要求。面轮廓度误差是描述曲面尺寸准确度的主要指标为轮廓度误差,它是指被测实际轮廓相对于理想轮廓的变动情况。
一、轮廓度公差的测量方法及计算方法的介绍
传统的面轮廓度测量误差的测量方法包括仿形装置测量、截面轮廓样板测量、光学跟踪轮廓测量仪测量。这 种测量方法要求做出理论轮廓样板后才能测量。
由于理论轮廓样板制作非常困难,因此该测量方法适合于一种黑件大批量生产过程中的检验。随着现在三坐标测量机的普遇运用,越来越多的企业多倾向于使用三坐标测量,测量精度高、效率快。
1、仿形装置测量
首先配备一些必要的辅助装置以及测量器具如百分表(千分表),通常我们选择
的测量器具的精度是被测量公差的1/3,才能满足我们的测量要求,调整被测雾件相对于仿形装置和轮廓样板的位置,千分表调需。仿形测头在轮廓样板上缓慢移动,由千分表读取示值并做好记录,记录的点数不少于10点,取其最大示值得2倍,即为面轮廓度误差值。在过去走访的很多企业,对二线检测人员进行调研时,很多人都会用此方法测量,但对于数据处理时,遇到了疑惑,得出的数据要不要再乘
以2? 今天笔者在这明确的告诉大家,需要乘以2倍。
2、截面轮廓样板(简称轮廓度样板法)
测量这种测量方法在批量生产中最为常见的,配以适当的量具如塞尺(专用)和辅助装置就可以了,我们把理论轮廓样板贴合在被霁件的表面,根据光除法估读法找到最大间隙处,用塞尺测其最大间隙。此最大间朦即为其轮廓度误差值,请读者一定要注意,不能将其最大间隙值乘以2倍。
3、光学跟踪轮廓测量仪(投影仪)测量
此方法适用于测量尺寸较小和薄的需件,在本案例-中不适用,在此也简单介绍一下,将被测轮廓,投影在投影屏上与极限轮廓相比较,实际轮廓的投影应在极限轮廓线之间,即为合格。这种测量方法不能得出具体数值,只作合格与否的判定。
4、三坐标检测方法
采用三坐标测量装置进行测量时无需轮廓样板,只需要被测霁件的CAD的3D模型(需件的三维设计图形),因此该测量方法可应用于任何场合且测量数据可靠。根据测量测头是否和零件表面接触可分为接触式与非接触式两类。
接触测量法以三坐标测量机测量为典型代表。三坐标测量机对环境(如:温度、温度、防振等)要求高。由于测量时测头在工件上要逐点测量,所以测量速度较慢,但是其测量精度高,适用于公差小,精度要求高的霁部件,另外要注意被测雾件的材质不能太较。
非接触测量法以结构光法为典型代表。该测量方法一次获取物体表面的数据(点坐标)多,测量范围大,对被测量物体的材质没有要求,特别适合于面积大且易变形的覆盖件类零件的测量。
其计算方法相同即测出若干个点的坐标值,并将测得的坐标值与理论轮廓的坐标进行比较,取其偏差值最大绝对值的2倍作为该零件的轮廓度误差值。
二、典型案例分析一(无基准要求)
首先,我们分析图1.这是我们做检测的第一步,面轮廓度要求0.02mm,整个曲面是球面,家根据要求,我们需要选择合适的测量方法和测量器具,针对本例,很显然不能用轮廓度样板,使用轮廓度样板法,普通塞尺的精度达不到,通常塞尺的最小测量精度0.02mm(量具的最小分辨率)>=1/3mm(被测要素的轮廓度公差值)。
同样用投影仪测最也是不合适的,图1需部件尺寸大且非薄壁件。那么我们用
仿形测量装置法进行测量配备轮廓度样板、千分表、固定和可调支承,调整被测零件相对于仿形装置和论廓样板的位置、千分调零。
彷形测头在轮算样板上缓慢移动至整段曲面,为了减小测整系统误逆, 我门尽量使指示计测头与仿形测头的形状-致,且垂直于理想轮廓方向上,由千分表读取示值并做好记录,记录的点数应不少于10点,取其最大示值的2倍,即为面轮廓度误差值。
值得注意的是: 整个曲面是球体,为了能够覆盖到整个曲面,我们需要每隔 120°测量一组数据。假设我们测量的数值第一组数
据ΔP1为 :
0.005 0.007 0.004 0.010 0.012 0.009 0.007 0.006 0.015 0.013
ΔP1max=0.015单位(mm)
第二组数据ΔP2为:
0.006 0.007 0.008 0.011 0.012 0.014 0.007 0.008 0.012 0.006
ΔP2max= 0.014 单位(mm)
第三组数据ΔP3为:
0.010 0.007 0.004 0.010 0.008 0.011 0.007 0.006 0.016 0.010
ΔP3max=0.016单位(mm)
因为ΔP3max>ΔP1max>ΔP2max
所以面轮廓度误差f=2xΔP3max=0.032 mm
接下来,我们用接触式三坐标进行测量,按照传统的三坐标测量方法:直接测量其整个球面或过球心的截圆,评价其半径,测量的数据如下:
80.004 80.008 80.012 80.013 80.015 80.005 80.004
80.010 80.015 80.009 单位(mm)
在评价报告里,输入标称值,测定值和偶差会直接读出的,面轮廓度误差即为一组数据中取其偏差最大值绝对值的2倍。
计算方法依据 GB/T1958-2004: ΔP=| 实际值-理论值|
ΔP的值:
0.004 0.008 0.012 0.013 0.015 0.005 0.004 0.010 0.015 0.009
ΔPmax=0.015mm
所以面轮廓度误差f=2xΔPmax=0030mm
二、典型案例分析一(有基准要求)如图2
由图2,我们采用传统的检测方法都是不行的,,从图形分析来看,有基准要求,根据曲线上的点坐标来判断整段曲线的轮廓度误差是否符合设计要求。
在这里我们只能借助三坐标测量机进行自动测量,那么我们需不需要导入数模呢?
不需要。首先我们建立坐标系,以基准A和B为基准,坐标建立以后,我们利用自动测量点,使用自动测量的优点是,省去了计算测头接触曲面的矢量角。测得的实际坐标可以直接参与计算了。
点1-点7的X轴实际坐标为X1~X7,Y轴实际坐标为Y1-Y7,Z轴坐标值不考虑。
点1-点7理论坐标(7.8,80.6)、(26.2,98.9))、(56.7,75.3)、(75.9,65.3)、(97.7,81.7)、(127,1024)、(142.99.9)
假设我们测量的点1-点7实际坐标分别为
(7.801,80.623)(26.232,98.901)(56.741,75.279)
(75.914,65325)、(97.68,81.689)、(126.998,102.384)、(141.985,99.973)
根据公式:
f-2×ΔPmax
ΔX、ΔY=实际坐标值-理论坐标值
△P—坐标偏差值
f--轮廓度误差值
根据公式计算:
△P1=0.023
△P2=0032
△P3=0046
△P4=0.029
△P5=0.016
△P6=0.016
△P7-0.023 单位(mm)
即△Pmax 为△P3
f=2×0.046=0.092mm
案例分析三(有基准要求)如图3:
由图3,我们可以看出,图形比较复杂,涉及到三维图,使用传统方法测量比较困难,用三坐标直接测量,但具体的点的坐标值又没有给出,那么我们可以使用三坐标的3D数模导入法,先导入需件 3D数模,再建立坐标系,利用拟合坐标系使实际的坐标系与数模坐标系重合,那么现在就可以测量了,把鼠标放到数模上点击,该点的理论值会显示在图形上,实际值就是测量后的坐标值,值得注意的是,此时要考虑XYZ的理论坐标值。在整段曲面上采点数为8--10点,根据公式:
计算出每一点的坐标佩差值,轮廓度误差值为最大坐标佩差的2倍,即
f=2xΔPmax
ΔX、ΔY、ΔZ=实际坐标值-理论坐标值
ΔP 坐标佩差值
fΔ 轮廓度误差值
【结束语】PC-DMIS测量软件当然具有自动计算功能,但笔者介绍的测量方法可以作为三坐标测量的补充和验证,供广大读者参考。
【参考文献】
GB/T1958-2004《产品几何量技术规范 形状和位置公差 检测规定》
GB/T17852-1999《形状和位置公差 轮廓的尺寸和公差注法》
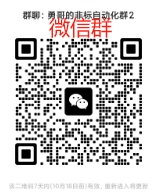
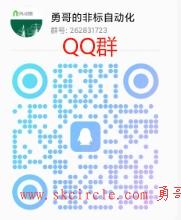